The turbine system is now widely used in the automotive industry, both energy saving and environmental protection, so it is recognized by users. As for how it works, today we’re going to talk about turbine systems.
The turbine system
The turbo system is one of the most common supercharging systems in supercharged engines.
If the unit is in the same time, to be able to more air and fuel mixture enforcement action (combustion chamber) is compressed into cylinder bums (small displacement engine to “breathe” and large displacement of the same air, improve the efficiency of volume), nature can be under the same speed to produce the engine air intake greater power output. It is like taking an electric fan and blowing it into a cylinder, forcing the wind into it to increase the volume of air in order to get more horsepower, only instead of using an electric motor, the fan is driven by the exhaust fumes from the engine.
Generally speaking, the engine in coordination with such a “forced intake” action, at least 30% to 40% of the extra power, such an amazing effect is the reason why turbochargers are so attractive. Moreover, achieving perfect combustion efficiency and a huge boost in power is what a turbo system can offer the most value to a vehicle.
The system comprises a turbocharger, an intercooler, an intake bypass valve, an exhaust by-pass valve, and a matching intake and exhaust pipe.
The connection mode of the turbocharger in the automobile is shown in the figure below:
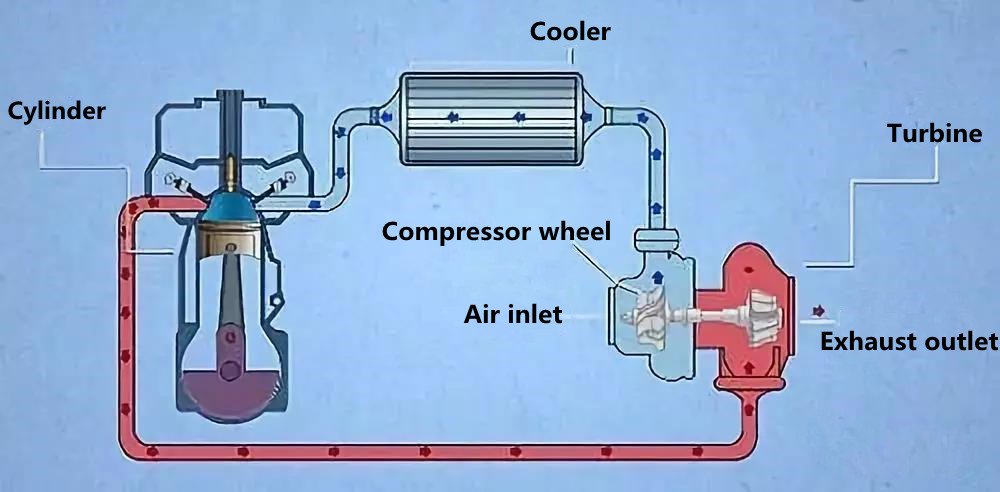
Power increase
General NA(natural intake) engine practice, can not escape to increase the throttle caliber or change the multi-throat direct injection so that high speed can be at the same throttle depth, get more air volume. But the effect of this method is limited after a certain number of revolutions. After all, NA engines take in air through a vacuum. There is a relative limit to the suction of air by vacuum at a constant cylinder volume.
Some NA engines use a high-angle camshaft (HICAM, to increase the intake and exhaust valve overlap Angle), which can achieve high power at high RPM, but the disadvantage is that the torque at low RPM is poor, and if the angle is too large, the engine will have the phenomenon of idle speed instability. So now a lot of new cars are using variable valve timing technology, with variable camshaft technology (such as VVTL-I, I-VTEC, MIVEC)…… In order to achieve a good balance between low torque and high horsepower.
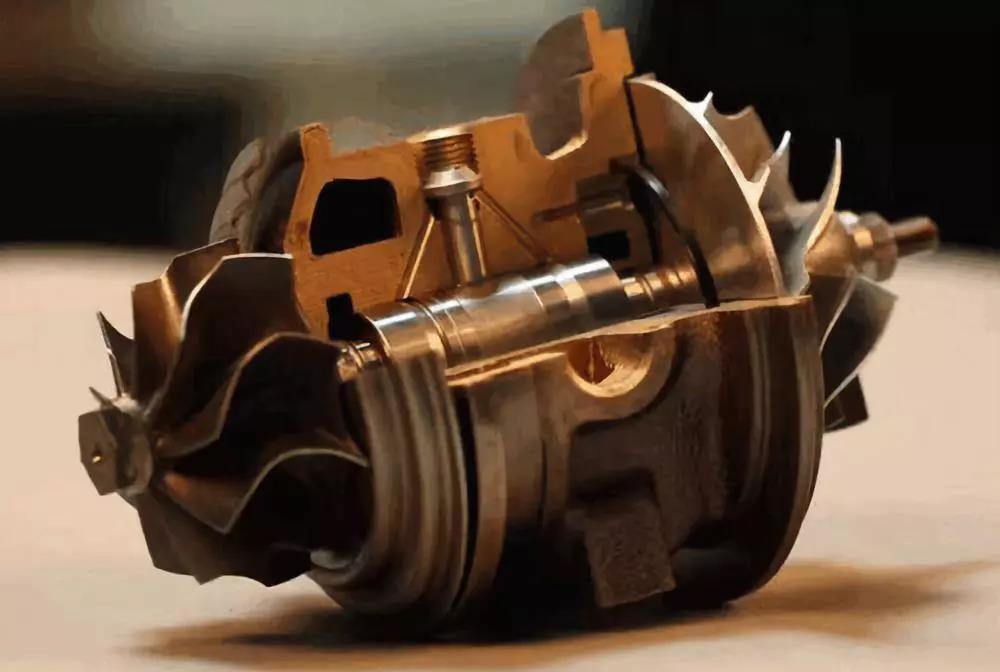
But even with all of the above methods, the intake efficiency of the engine is improved by at most 60%. The NA engine was never immune to its fate — air was drawn passively into the cylinder. In other words, the air needed by the engine is completely dependent on the negative pressure generated by the piston descending, and even when the cylinder is full of air, the pressure in the cylinder is less than or equal to one atmosphere. As a result, the liter power of the NA engine is still far from being able to force air and fuel into the cylinder, and a supercharged engine with more than twice the horsepower can easily be obtained.
Turbocharger bearing
The bearing structure of the turbocharger is related to the reliability and durability of the turbine. Turbocharger bearings are mainly divided into two categories, one is floating bearings (commonly known as Bossi bearings), the other is ball bearings. Floating bearing is actually a ring sheathed on the shaft, and there is a gap between the ring and the shaft and the ring and the bearing seat, forming a double-layer oil film. When the supercharger works, the bearing rotates between the shaft and the bearing seat. Therefore, we can find the disadvantages of floating bearings: high rotation resistance of the turboshaft, high oil pressure and quality requirements, and unstable dynamic control of the turboshaft.
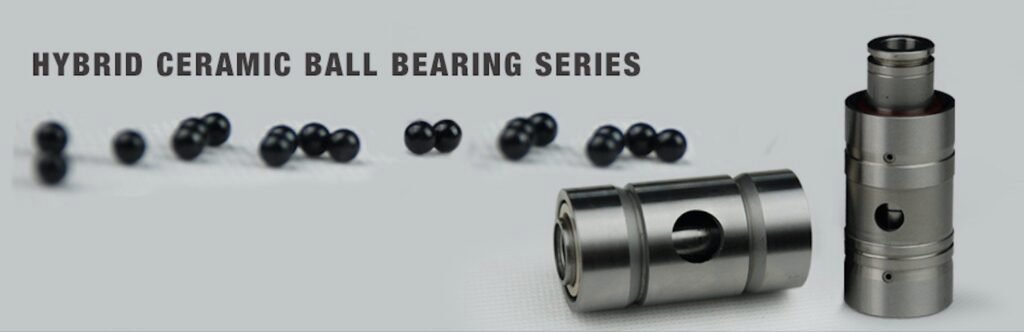
And the recent emergence of Ball Bearing (Ball Bearing) gradually become the trend of the development of the turbine shaft. As the name suggests, ball bearings are installed on the turbine shaft ball, instead of oil to become bearings. Ball bearings have a number of benefits: less friction, hence better turbine response (reduced turbine hysteresis), and better power extraction at the limit; It has a more stable dynamic control over the rotation of the turbo shaft (the traditional one is to rely on oil to do the bearing, and the stroke is floating); The oil pressure and quality requirements can be relatively reduced, which indirectly improves the service life of the turbine. But its disadvantage is that the durability is not as good as the traditional Bossi bearings, about 70,000-80000 kilometers to the life limit, and not easy to maintain, maintenance is expensive. So turbine manufacturers that value durability, such as KKK, do not offer this type of turbine.