Keywords: Hybrid ceramic ball bearings, Ball Bearings, Angular Contact Ball Bearing
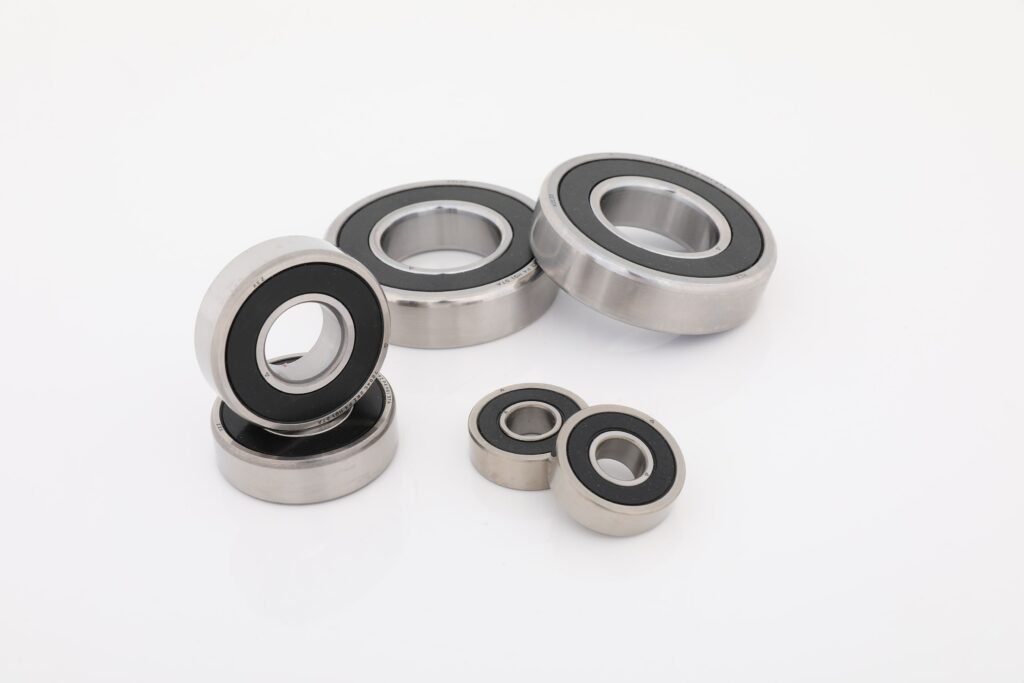
Direct lubricated bearing
In the case that grease lubrication can not meet the requirements, direct lubrication bearing is the best choice to improve the spindle speed. Directly lubricated bearings ensure that the lubricant is supplied closer to the rolling contact area. It is realized through the circumferential lubrication groove and the radial lubricating oil hole on the outer ring of the bearing. The precision 0 type sealing ring makes the bearing sealed in the bearing seat. Directly lubricated bearings can achieve extremely high speed. Its special power density is not the only advantage of this design. It also reduces the cost of peripheral junction elements. This saves space and reduces costs.

Hybrid ceramic ball bearings
There is an increasing demand for bearings with steel inner and outer rings and ceramic balls in the market. Originally used only at high speeds, hybrid ceramic ball bearings are now also used at low speeds. The reasons are as follows:
- Its durability and reliability are high
- Significantly extend the service life of grease
Compared with the steel-to-steel material combination, the load on the lubricant can be significantly reduced by using steel-ceramic materials. The ellipse has a smaller stress deformation area, thus reducing the stress on the lubricant.
Because of the different materials used, there is less chance of adhesion. Similarly, the thermal stress is reduced compared with a bearing made entirely of steel. The use of ceramic ball bearings greatly increases the speed, thus expanding the range of grease lubrication.
The overall cost of the system, both in terms of design and actual operation, is substantially reduced.