Keywords: spindle bearing, XEZ ball bearing, machine tool spindle bearing
The use of engraving machine friends know that engraving machine spindle is an important part of the engraving machine, engraving machine must start a major part of the operation, engraving machine spindle is often a problem is easy to bad bearings, some spindle bearings with less than a few months are broken, there are many reasons for the problem.
We also often receive some users’ consultations, said their spindle motor why to feel particularly easy to damage it, in fact, the reason for the spindle is easy to break more, and the spindle itself and the use of conditions have a close connection. XEZ Ball Bearing gave you the following main reasons.
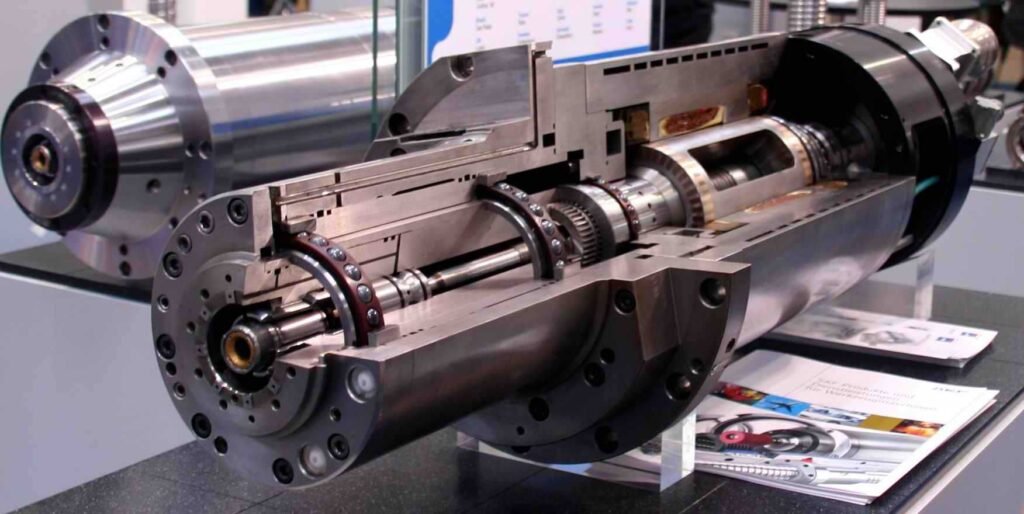
1. The quality of the engraving machine spindle.
In the case of engraving machines everywhere, engraving machine spindle quality is uneven. Buying a particularly poor quality spindle in a high intense working environment, easy to break is the inevitable result. So users friends in the purchase of engraving machine spindle motor must choose a formal and good reputation of the company, must not covet a cheap buy inferior or even fake and refurbished motorized spindle.
2.Engraving machine main shaft use problem.
Because of the fierce competition in the engraving machine market, the major engraving machine manufacturers are attracting customers through the advantage of low prices. This has caused manufacturers to cut corners in order to save costs, one of the most representative is that many manufacturers use woodworking spindles to use in stone engraving machines and other equipment. Because the cutting force of stone carving is far greater than that of wood carving, and the need to increase water cooling and other liquids in the process of stone carving, wood spindle design requirements do not have waterproof conditions. Therefore, such a spindle is particularly vulnerable to breakage.
3. The engraving machine spindle cooling system is poor.
The cooling system of the main shaft of the engraving machine is mainly divided into air cooling and water cooling. Comparatively, the cooling effect of water cooling is better than that of air cooling. If the water cycle is not good for a long time or the water cycle is forgotten, the thermal effect will appear after the machine works for a long time, friction increases, and the pressure of the bearing becomes large and easy to break down.
4. The engraving machine’s continuous working time is too long.
The speed of the engraving machine spindle can reach 24000 revolutions per minute. In continuous high-intensity work, the overload operation time is too long to damage the spindle, generally not more than 12 hours.
5. Engraving machine operation is improper.
When customers are working, they start to carve when the spindle speed has not reached the specified working speed, which is easy to cause bearing damage; In the engraving of different material resistance is not the same, did not adjust the speed in time will be the engraving machine main shaft.
6.The main axis in winter anti-freezing measures are not in place.
Every year in winter, water is easy to freeze because of the low-temperature winter. If the user does not timely discharge the residual water inside the main shaft after the end of the engraving machine, due to the principle of thermal expansion and contraction, the volume of the residual water will become large and freeze the main shaft. Therefore, in some northern regions, we suggest that antifreeze should be added in winter to prevent unnecessary losses caused by freezing damage to the main shaft.

We hope that the majority of engraving machine customers pay attention to these problems, maintain the life of the spindle, improve work efficiency, and save expenses.
Related articles on spindle bearings also include: Lubrication mode and installation steps of machine tool spindle bearing