Keywords: Cage, lubrication, roller, temperature rise, spindle bearing, angular contact ball bearing
In order to further improve the performance of machine tools, it is necessary to improve the performance of spindle units (one of the main units affecting the performance of machine tools), and spindle bearings play a key role. Here are three kinds of spindle bearings developed.
With the increasing demand for high-precision machining, bearings need to have high speed, high stiffness and low-temperature lift performance. Spindle bearings are widely lubricated with grease and oil and gas. In fact, grease lubrication is usually used for ease of operation and simplification of spindle structure. At high speeds and where high stiffness is important, oil-gas lubrication is the preferred method. Firstly, two kinds of grease-lubricated spindle bearings developed are introduced.
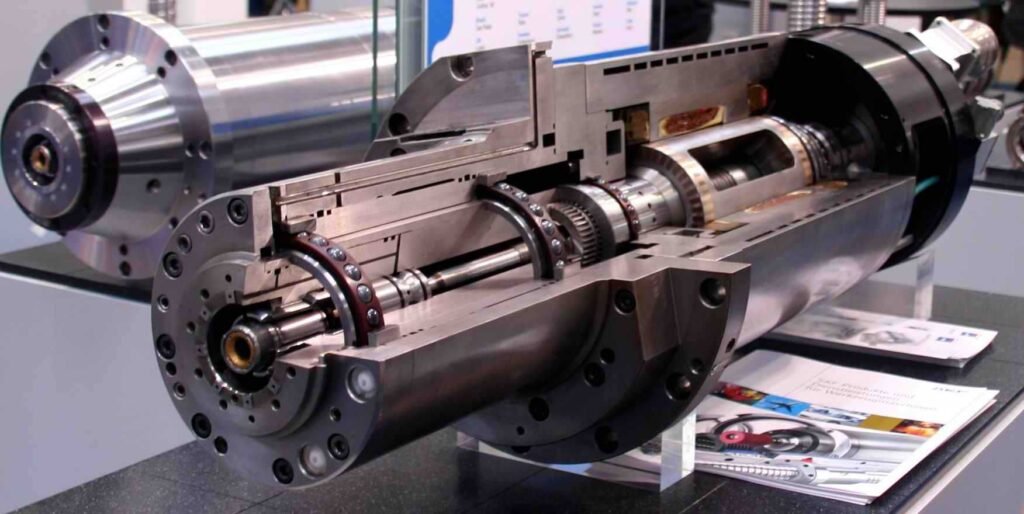
| 1. grease lubricated, high stiffness, low temperature rise double row cylindrical roller bearings
The typical bearing layout of the lathe spindle unit. In order to ensure radial stiffness, grease-lubricated cylindrical roller bearings are usually used in lathe spindle front bearings. Brass cages were originally used, but sometimes during operation, metal chips would come into contact with rollers, reducing grease performance. Therefore, resin cages are used in some high-speed applications. Polyamide resin was initially used, but as spindle operating conditions became more demanding, the cage broke again.
1.1 Analysis of Cage Fracture Rapid acceleration, deceleration and heavy loading lead to the advance or lag of rollers, resulting in tension and compression loads along the perimeter of the cage beam, resulting in cage fracture.
1.2 Cage structure improvement
1) Cage shape: from the original window cage to claw cage; Cage material: From polyamides to super engineered plastics By using the claw cage, can reduce the tension and compression load on the cage beam circumferential stress. FEM analysis shows that the maximum principal stress of the new cage product is about 1/3 of that of the conventional product when the roller leads or lags behind to produce a circumferential load.
2) For the roller guided claw cage, the radial deformation (expansion) of the claw is caused by the centrifugal force acting on the cage when the bearing rotates, which leads to the larger guide gap of the cage during rotation. As a result, the contact stress between the cage and the roller increases, resulting in fever. Therefore, in terms of materials, super engineering plastics are selected as anti-fracture to effectively prevent claw deformation; In order to reduce the mass of the claw, the length of the claw is shortened. The durability and temperature rise tests prove that the newly developed bearing has good performance (durability increases by more than 3 times and temperature rise decreases by 24%).
| 2. grease lubricated, low-temperature Angle rising contact ball bearings
In order to further reduce the temperature rise, it is necessary to reduce the stirring resistance of grease and the contact resistance of the cage and ball. By increasing the clearance between the cage and inner ring, the fluidity of grease is improved and the stirring resistance is reduced. Change the contact point of the ball in the pocket hole of the cage (the shape of the pocket hole changes), instead of 3 contact points of the ball in the pocket hole of the cage of the conventional product, change the contact point of the ball in the pocket hole of the cage to only 1 contact point. The temperature rise test shows that compared with conventional products, the temperature rise is reduced by 15%.
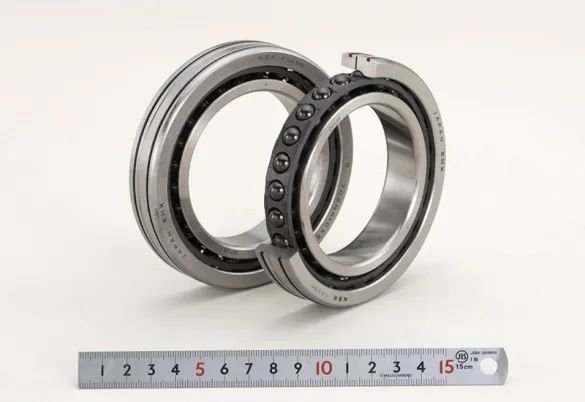
| 3. The ultra-high-speed angular contact ball bearing
Developed by NSK is equipped with the newly developed SURSAVE™ cage, which achieves low NRRO (non-repetitive runout) (NRRO decreases by 50% at high speed), low torque (torque decreases by 20%) and high speed (DM. N value reaches 3 million).
The cage adopts PPS (polyphenylene sulfide) reinforced material, which has better structural strength.
The design and development of the three special spindle bearings are mainly through the improvement of cage structure and material, so as to improve cage rigidity and reduce friction and meet the high-performance requirements of bearings under the premise of maintaining the basic function of the cage. It also reflects the key and importance of maintaining the design in the design of high-speed bearings.