Keywords: spindle bearing, machine tool spindle bearing
Machine tool spindle bearing is the spindle bearing of precision machine tools and similar equipment, which can guarantee the working accuracy and performance of precision machine tools. The correct configuration of spindle bearings refers to the combination of bearing types and the arrangement of front and rear bearings. The different configuration determines the different load capacity, running speed, stiffness, temperature rise and service life of the machine tool spindle.
Maybe you are interested in Which kinds of bearings are commonly used for machine tool spindles?
In particular, the influence on the stiffness and temperature rise is more significant, so the spindle bearing should be reasonably configured according to the requirements of the working characteristics of the machine tool. In terms of function and structure, spindle bearings can be divided into rolling bearings and sliding bearings.
Running-in is the purpose of the operation in order to make the bearing before officially make Angle, make its roller and race through the running-in, can have good contact conditions, to maintain the accuracy of bearings have good contact, and to avoid bearing the beginning in high-speed and heavy-load roller and raceway damage when using, thus improve the life and precision of the bearings’ as a result of the tapered roller bearing is not completely rolling contact, There is sliding between the end face of the roller and the shoulder of the inner ring. If the contact condition is not good, it is easy to appear the phenomenon of occlusion damage. Therefore, more attention should be paid to the running and running of this kind of bearing.
Mechanical spindle refers to the shaft on a machine tool that drives the workpiece or cutting tool to rotate. Usually by the spindle, bearing and transmission parts (gear or pulley) and other components of the spindle. The machine is mainly used to support the transmission parts such as gear, belt pulley, transfer movement and torque, such as machine tool spindle; Some are used to clamp the workpiece, such as the mandrel. Most machine tools have spindle parts, except planers, broaching machines, and other machines whose main motion is linear. The motion precision and structural stiffness of spindle components are important factors to determine the machining quality and cutting efficiency.

Performance comparison of spindle bearing types
Spindle bearing is an important part of the CNC machine tool spindle. In the process of spindle transmission, it can support the rotation of the mechanical body and reduce friction. Bearing because of its type, structure, configuration and accuracy, as well as installation, adjustment degree of good or bad will have a direct impact on the performance of spindle components. In terms of function and structure, spindle bearings can be divided into rolling bearings and sliding bearings. According to the pressure mode of oil film generation, sliding bearings can be divided into the hydrodynamic bearing and hydrostatic bearing.
The rotating accuracy of rolling bearings in general or good, and it may be high when working without clearance or preload. The stiffness is average or good, only related to the bearing type, and so is the carrying capacity. Poor vibration resistance performance, low and medium speed performance is good, high speed by fatigue strength, centrifugal force, temperature rise and other factors limited. Friction loss is small, noise is large, life is limited by fatigue strength. Production, use and maintenance are relatively simple, have been standardized and serialized, can be low cost mass production.
The rotating accuracy of the dynamic pressure bearing in general, but the accuracy is good. Stiffness and bearing capacity are high and increase with the increase of speed and load. Good seismic performance, medium and high-speed performance are good, low speed because can not form oil film, no bearing capacity, ultra-high-speed by temperature rise limit. Small friction loss, no noise, long life when infrequent start. The production cost is low, but the technical requirements are high, the factory’s needs to make, use and maintenance is also more troublesome.
The hydrostatic bearing has high rotation accuracy and good retention. Stiffness and bearing capacity are very high, independent of the speed and load, and related to the throttling form and the relative pressure difference of the oil chamber. Excellent anti-seismic performance, suitable for various operating speeds, especially low speed and ultra-high-speed operation. Very small friction loss, no noise, very long life. In addition to its own cost, but also need a set of oil supply equipment, so the total cost is high, and the production process requirements are also high, the factory to make, use and maintenance more troublesome.
When choosing the type and combination of bearings to be used, the requirements of spindle components in all aspects, as well as the supply of bearings, costs, installation and debugging difficulties and other factors should be comprehensively considered. Under normal conditions, the spindle should be preferred rolling bearings, especially for vertical spindle, only when the spindle is placed horizontally, and the surface roughness of the workpiece is small, the sliding bearing is used.
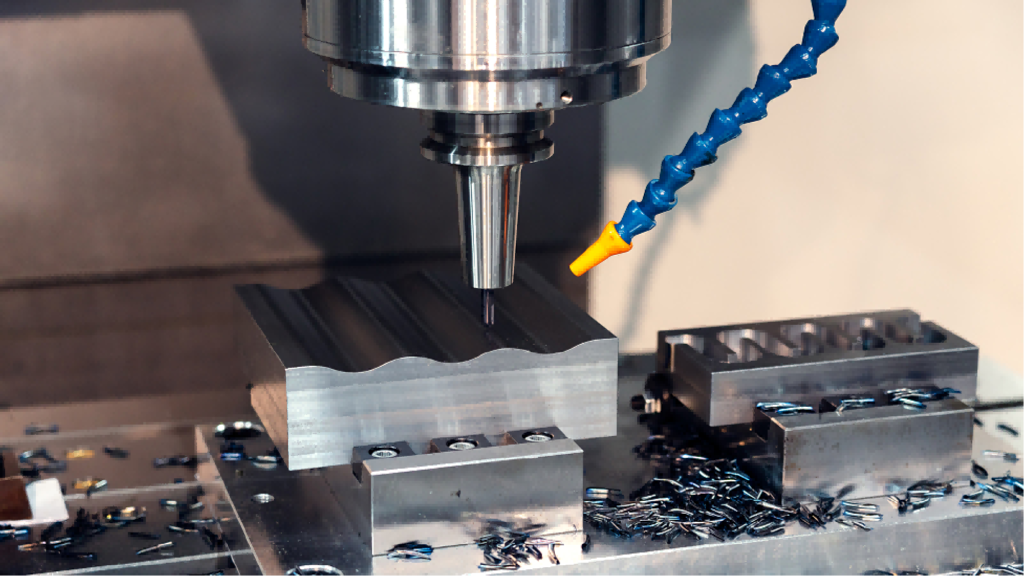
Lubrication mode of spindle bearing
- The sequence of filling grease after cleaning the bearing
Different filling methods of grease will cause instability of temperature rise, abnormal temperature rise, long time of initial running-in, and even burn during the initial running-in operation. Therefore, it is necessary to use appropriate grease and appropriate filling amount to fill correctly according to the use conditions.
(1) Confirmation matters before filling
Verify that there is no residual foreign body inside the bearing. It is suggested that bearings for high-speed spindle should be cleaned, degreased, and then filled with grease.
In other applications, it is also recommended to remove the anti-rust oil attached to the inside of the bearing.
(2) when filling the grease
To fill an appropriate amount of grease, it is recommended to use a grease injector. It is best to use a grease injector that uses a readable fill number.
(3) the amount of grease filling
Recommends for filling amount of precision bearing grease:
High speed spindle with angular contact ball bearings, space volume 15/20%
Cylindrical roller bearings for high speed spindles, 10% of space volume. %
Ball bearings for motor, 20%~-30% of space volume
2, the ball bearing grease filling mode
(1) evenly fill the grease between each ball. In the case of outer ring guided phenolic cages, it is recommended that the cage guide surface also be thinly coated with grease.
(2) rotate the bearing by hand, so that the grease evenly enters the raceway surface, cage interior, between each ball, guide surface and other places, so that the grease is filled with the inner space of the bearing.
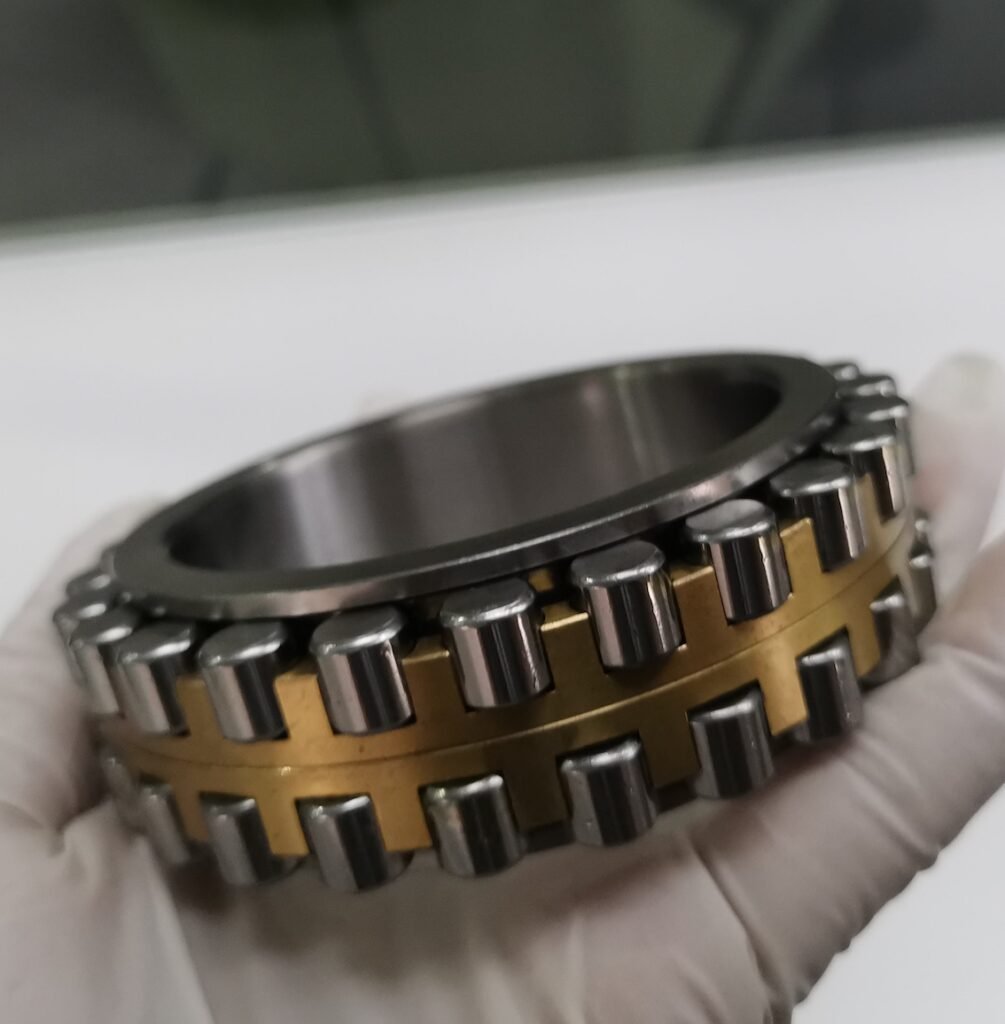
- Grease filling method for cylindrical roller bearings
(1) the filling amount of 80% of the grease, evenly coated on the rolling surface of the roller. At this time, it is recommended not to smear too much grease on the inside of the cage. The grease inside the cage is difficult to diffuse in the initial running-in operation stage, which will increase the temperature and prolong the running-in operation time.
(2) the grease on the roller raceway surface will spread to the end face of the roller, the contact part between the cage and the roller, as well as the entrance of the pocket part so that the grease is evenly distributed to the whole bearing.
(3) the filling amount of 20% grease is uniformly thin coated on the outer ring raceway surface that will be installed on the intake bearing seat.
Installation of spindle bearing
Whether the installation of bearings is correct or not directly affects the accuracy, life and performance of bearings. Therefore, it is hoped that the design and installation department should fully discuss the installation of bearings and install them in accordance with the operating standards. The operating standard items are as follows:
- Cleaning of bearings
In order to prevent dust and rust during transportation and storage, the bearing surface is coated with anti-rust oil when the products are shipped.
After unpacking the package, the first thing to do is to wash away the anti-rust oil. (bearings with filled grease or sealing ring do not need to be cleaned)
1) bearings generally use kerosene or gasoline as cleaning fluid.
2) Separate the cleaning tank according to rough cleaning and fine cleaning, and put a metal net on the bottom of the tank respectively, so that the bearing does not directly contact the dirt in the cleaning tank.
3) in the rough washing tank, try to avoid turning the bearing, and roughly remove the dirt attached to the surface of the bearing with a brush, then put it in the fine washing tank.
4) in the fine cleaning tank, the bearing is gently rotated to clean. The cleaning oil in the fine washing tank must be kept clean at all times.
5) degreasing after cleaning, if it is grease, then fill the grease. If it is oil-gas lubrication, try to install it on the spindle under the condition that the bearing does not rotate. (At this point, the bearing surface and interior coated with a thin layer of lubricating oil, the effect is better.)
- Check the size of relevant parts
1) Check the shaft and bearing housing
A. Shaft and bearing housing should be cleaned. No scars, burrs, burrs, etc. are allowed on the surface of bearings and spacers.
B. Check the dimensions of the shaft and the bearing seat to confirm whether it conforms to the tolerance with the inner and outer diameters of the bearing.
C. Measurement (including installation) N shall be carried out in a constant greenhouse. When the temperature of the object to be measured is in a stable state, use a micrometer or internal dial gauge to measure. (Multiple measurements must be made to check for obvious size differences.)
2) Check the ring
The parallelism of the spacer arranged on the spindle shall be controlled below 0.003mm. The poor parallelism of the spacer will lead to the tilt of the bearing, resulting in poor accuracy, noise and other problems.
- Installation of bearings
Install the bearing that has been filled with grease (grease lubrication) or the bearing that has been degreased and cleaned (oil lubrication) to the spindle or bearing seat.
The installation method is different according to the fit of the inner and outer ring. For machine tool bearings with a majority of inner ring rotation, the inner ring mostly adopts interference fit, and cylindrical bore bearings generally adopt the hot charging method.
The outer ring adopts clearance, which is easy to install. Sometimes, the method of heating the bearing seat is also used to make the installation easier.
Tapered bearing is the inner ring is directly fixed on the conical shaft, used for high-speed rotation, must control the radial clearance during installation, it is recommended to use GN gauge.
1) Installation of cylindrical bore bearings
A. Press in method
Small bearings are widely used in the press pressing method, with a pad against the inner ring, with the press gradually suppress the inner ring close contact with the shaft shoulder. (Install the outer ring pad on the inner ring pad block, which will cause indentation and crush on the surface, so it is absolutely prohibited) In addition, it is best to grease the surface in advance when operating. The hammering method of mounting with a hammer is prohibited for precision bearings.
For separable bearings such as cylindrical roller bearings and tapered roller bearings, the inner ring and outer ring can be installed on the shaft and bearing seat respectively. When assembling the inner and outer rings installed separately, it is important not to deviate from the center of the two rings. It is very important to assemble the inner and outer rings slowly. If pressed hard, it may cause sticking on the rolling surface.
B. Method of hot loading
Bearings with large interference require great pressure when pressed in, so it is difficult to install. Therefore, the hot charging method of heating and expanding the inner ring of the bearing and then loading it on the shaft is widely used. Using this method will not add undue load to the bearing, and the operation can be completed in a short time.
The heating temperature of the bearing shall be referred to as the normal size and the required interference amount. Hot loading operation should pay attention to the following points:
(1) Heat the bearing to more than 120℃.
(2) in order to avoid the installation difficulties caused by inner ring cooling during the bearing installation process. The bearing should be heated to a degree of 20℃-30℃ higher than the required temperature.
(3) after hot loading, the bearing gradually cooled down, and the width direction contracted at the same time. Therefore, the shaft nut or other suitable method should be used to tighten it so as to prevent the clearance between the inner ring and the shaft shoulder.
2) Matters needing attention when installing angular contact ball bearings
Angular contact ball bearings, due to structural reasons, a single bearing can only bear the load in one direction. Therefore, when installing a shaft or bearing seat, it is very important that the external load be applied only to one of the tolerable loads and not to the other.
When combining bearings, for back-to-back combination and face-to-face combination, they are loaded into the shaft or bearing seat in a different order, be sure to pay attention to them.
A. Back-to-back combination
(1) Install the bearing on the shaft
(2) tighten the shaft nut and apply pre-tightening.
(3) Install the shaft and bearing into the bearing seat and fix it with the gland.
B. Face to face combination
(1) Install the bearing into the bearing seat.
(2) Tighten the gland and apply pre-tightening.
(3) Install the shaft into the inner ring of the bearing and tighten the shaft nut.
When disassembling, proceed in reverse order.
- Fastening of bearings
A. Fastening of inner ring
In order to fasten the bearing inner ring on the shaft, the thread is generally processed on the shaft, and the nut is used for fastening. Although the verticality between the threaded part and the end face of the nut is very important, even for a single nut with high precision, the clearance between the shaft and the nut can cause deviation and tilt during fastening. This will lead to the bending of the shaft and bearing, so in order to ensure the rotation accuracy of the shaft, it must be adjusted. Nuts should be tightly tightened to prevent loosening.
In high speed and high precision spindle, in order to avoid the unbalance caused by nut tilt or thread clearance when the nut is fastened, the shaft sleeve fixing method is mostly used, and the axial fixing is carried out by the large surplus of the inner diameter of the shaft and the shaft sleeve. But compared with the nut fastening, it is easier to loosen under continuous operation, so it must be checked regularly.
When a wide spacer is placed between the combined angular contact ball bearings, if the tightening force of the nut is too large, the inner spacer will be deformed and the preload during installation will be greater than the set value.
B. Fastening of the outer ring
To secure the outer ring in the axial direction, the gland is usually secured with bolts. If the fastening amount is too large or uneven, the outer ring raceway surface is easier to produce deformation. It is suggested that the gap between the gland and bearing seat end face should be adjusted between 0.01~0.05mm.
Note that when running at high speed, the interference of bearing and shaft increases, so does the required pressing force, and the fastening force of the nut must be increased accordingly.
When the ball screw support is used for angular thrust contact with the ball bearing, the tightening force of the nut is recommended to be 2.5~3 times the pre-tightening force